How Often Should NDT Instruments Be Inspected?
July 10, 2025
Non-destructive testing (NDT) is crucial for ensuring the safety and reliability of materials, equipment, and structures in various industries. To maintain the accuracy and effectiveness of NDT instruments, regular inspections and calibrations are necessary. In this blog, we will discuss how often NDT instruments should be inspected, why these inspections are essential, and how they contribute to the reliability of your testing processes.
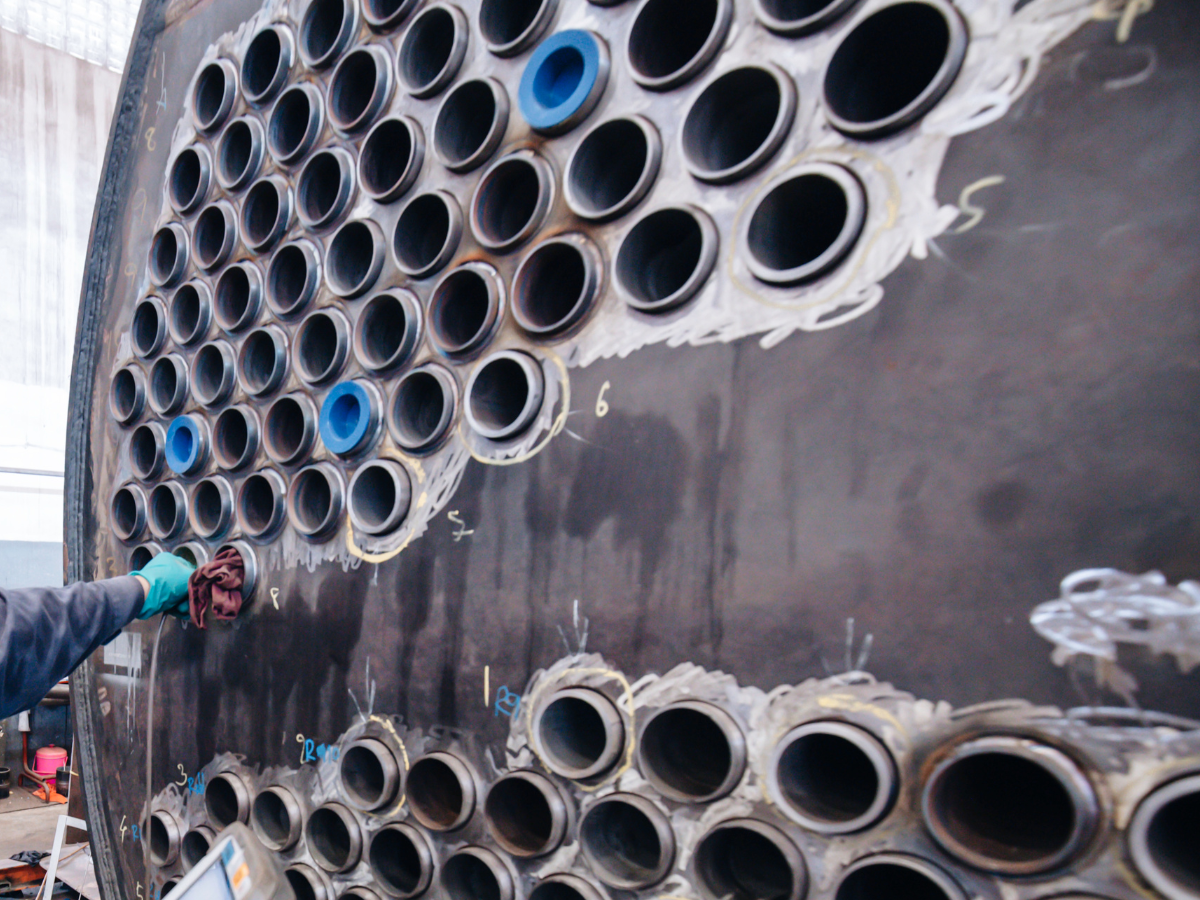
1. The Importance of Regular Inspections for NDT Instruments
NDT instruments play a critical role in evaluating the integrity of materials without causing damage. Whether you're using ultrasonic testing, radiography, or eddy current testing, NDT instruments must be accurate and in optimal condition to provide reliable results.
- Accuracy: Regular inspections ensure that your NDT instruments are calibrated correctly and provide accurate results, which is crucial for the safety of personnel and structures.
- Compliance: Many industries have strict regulations regarding the maintenance and calibration of NDT instruments. Regular inspections help ensure that your equipment complies with industry standards and regulations.
- Preventing Failures: Routine inspections can help identify potential issues before they become critical problems, reducing the risk of equipment failure and costly downtime.
By scheduling NDT instrument inspections regularly, you can maintain the quality of your testing and prevent inaccurate results.
2. Factors Affecting Inspection Frequency
The frequency of NDT instrument inspections can vary based on several factors. Understanding these factors can help you determine the ideal inspection schedule for your specific instruments.
- Type of Instrument: Different types of NDT instruments may require different inspection frequencies. For example, portable ultrasonic thickness gauges may need more frequent checks than stationary radiographic equipment.
- Usage: The more frequently an instrument is used, the more often it needs to be inspected. Instruments used in high-intensity environments or for critical testing may require more frequent inspections.
- Environmental Conditions: Instruments used in harsh or extreme environments, such as those exposed to high temperatures, moisture, or corrosive chemicals, may require more frequent inspections to ensure they remain in working condition.
Taking these factors into account will help you develop an inspection schedule that aligns with the needs of your NDT instruments.
3. Industry Guidelines for NDT Instrument Inspections
Industry standards and guidelines often provide recommendations for how often NDT instruments should be inspected. These guidelines are designed to ensure that testing is done accurately and in compliance with safety regulations.
- ASNT (American Society for Nondestructive Testing): According to ASNT, NDT instruments should undergo periodic calibration and performance checks to ensure their accuracy. The frequency of inspections can depend on the instrument's usage and the environment.
- ISO Standards: The International Organization for Standardization (ISO) sets guidelines for NDT instrument calibration and inspections. Following these standards ensures that your instruments meet the required quality assurance levels.
- Manufacturer Recommendations: Always refer to the manufacturer’s guidelines for your specific NDT instruments. Manufacturers typically provide recommendations for inspection intervals and maintenance procedures based on the design and intended use of the equipment.
Staying up-to-date with industry standards helps maintain compliance and ensures that your NDT instruments perform as expected.
4. Common NDT Instruments and Recommended Inspection Intervals
Different NDT instruments have varying inspection requirements based on their function and sensitivity. Below are some common NDT instruments and recommended inspection intervals.
- Ultrasonic Testing (UT) Instruments: These instruments require calibration checks at regular intervals. For high-usage applications, a calibration check may be necessary every 6 months. For less frequent use, yearly inspections may be sufficient.
- Eddy Current Testing (ECT) Instruments: Eddy current instruments also need regular checks for accuracy. It’s typically recommended to inspect these instruments annually, with more frequent inspections if used for critical or high-intensity applications.
- Radiographic Equipment: Radiographic testing equipment often requires comprehensive inspections and calibrations at least once a year, especially if the equipment is used in high-stakes testing scenarios.
- Magnetic Particle Testing (MT) and Dye Penetrant Testing (PT) Equipment: For MT and PT instruments, regular cleaning and checks should be conducted every 6 months, with calibration checks every year.
The recommended intervals may vary depending on the manufacturer’s guidelines, but understanding the general inspection schedules for each instrument can help ensure reliability.
5. Benefits of Regular NDT Instrument Inspections
Regular inspections and calibration of NDT instruments offer several key benefits:
- Enhanced Accuracy: Regular inspections help maintain the accuracy of your equipment, which is crucial for detecting potential defects and ensuring the safety of critical systems.
- Reduced Downtime: By identifying and fixing small issues early, you can avoid costly repairs and unexpected downtime, ensuring that your instruments are always available when you need them.
- Extended Equipment Lifespan: Regular maintenance and inspection of NDT instruments can help extend their operational lifespan by preventing wear and tear from accumulating over time.
- Compliance and Safety: Regular inspections ensure that your instruments meet safety and regulatory standards, protecting both personnel and the public.
By prioritizing regular inspections, you can ensure that your NDT instruments remain in top working condition, helping to maintain the safety and reliability of your operations.
Conclusion
Regular inspections of NDT instruments are essential to ensuring the accuracy, reliability, and compliance of your testing equipment. The frequency of inspections can depend on factors such as the type of instrument, frequency of use, and environmental conditions. By following industry guidelines and manufacturer recommendations, you can keep your NDT instruments in excellent condition, ensuring they provide accurate and reliable results.
At Steel City NDT, we offer comprehensive calibration and maintenance services for a wide range of NDT instruments. Contact us today to schedule an inspection or learn more about how we can support your NDT equipment needs.